What is the problem with electrostatics? From an atomic point of view, all neutral materials, such as plastics, paper, and other insulators, neutralize the positively charged nuclei of each atom and the negatively charged electron cloud, when the material passes through friction. After the contacts are separated, the electrons in the insulating material will be released to the surface of the material. For example, in the middle school physics, the glass rods were rubbed with silk, and static electricity generated on the glass rods lifted the scraps. The electron-reduced material surface is positively charged, while the electron-added material with excess electrons is negatively charged. If the electron-reduced material is supplemented with negative electricity and the electron-increased material is supplemented with positive electricity, the two materials are in balance between positive and negative electricity. The two materials are neutral.
In the printing of optical discs, so-called screen printing is a process in which ink is transferred to a substrate by a screen and a squeegee moving under a certain squeegee pressure. The screen (screen) and the squeegee (polyurethane scratch) are insulators. In the screen printing, they are rubbed against each other in the position, especially when the humidity is low, static electricity will affect the surface charge of the substrate. Distribution status. In particular, insulating materials, such as Pc substrates for optical discs, PET sheets for touch opening, and PVc for name and signage, PP, PE for plastic bottles, etc., are basically insulators, and they are not noticeable in screen printing operations. Static electricity will be produced. For example, when using a screen printing membrane switch to decorate the ink, because the PET film base is after the production, the surface is covered with a layer of PVC and other self-adhesive films to protect its surface, so that it will not scratch in the cutting, packaging and so on. However, after screen printing, the protective film must be peeled off before screen printing. Often, some operators remove the film at a very high speed. Do you not know that the protective film and the PET sheet are rapidly separated at the instant of quick release of the film? In the process, static electricity is generated on the surface of the PET sheet, especially under low humidity. As a result, the ink on the edge of the handwriting on the screen printing has flying hair, and the fluffy pattern-like ink on the transparent PET sheet sinks to the quality problem. This is a typical example, which has caused great confusion to the screen printing shop of the membrane switching unit.
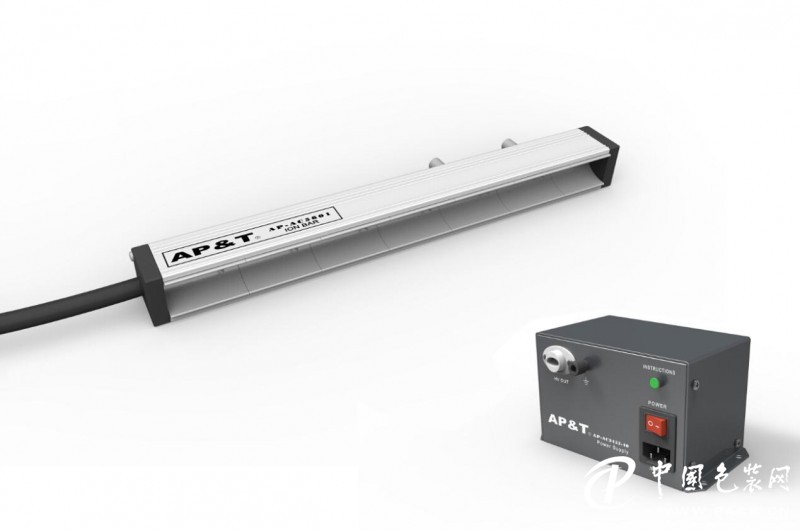
The model AP-AC5601 ion bar in the picture above can be used to eliminate static electricity during the screen printing process
First, because of the existence of static electricity, due to the production difficulties caused by static electricity in printing, the performance in screen printing is:
1. After silk screen printing, the ink on the blotting is pulled up with the screen plate, and the “flying†shape of the ink wire is disconnected after the workpiece is removed.
2. During overprinting, the ink and the edge of the ink of the previous and the next color are mutually exclusive and do not fit well, so that the ink cannot be printed between two inks.
3. In screen printing, the workpiece sticks to the screen, especially to the screen at the end of the screen.
4. Printing materials stick together
5. During the squeegee process, the ink spreads on the screen and the cakes stick together.
6. Dust is sucked on the substrate, and ink is missing after screen printing, pitting, rough surface, etc.
The above problems are mainly caused by the presence of static electricity. However, sometimes the presence of static electricity is also related to the fact that the printing process does not meet the requirements. For example, when the humidity is low and the amount of solvent in the ink is insufficient, the humidity in the air is low and the static electricity cannot Through the transmission of moisture, at the same time, the ink solvent is small, and the viscosity is large. With such a large viscosity, the ink itself naturally generates a drawing; if the printing speed is faster during the screen printing process, the squeegee and the screen strongly rub against each other to generate static electricity. Especially in the case of high-tension screens, when the squeegee pressure on the screen is high, the squeezing speed of the squeegee on the screen can be the most likely to cause the occurrence of static electricity. It is often said that frictional electrification is the reason.
Screen printing because of the existence of static electricity can cause many quality problems, and even printing can not continue, then how to avoid and eliminate static electricity in screen printing?
First of all, from the process conditions of the wire mesh itself, under the high tension of the screen, reduce the mesh distance as much as possible. When the net pitch is reduced, the pressure of the scraper is reduced, and the scraper reduces the possibility of static electricity generation due to the friction of the screen plate. In the screen printing of the optical disc, in order to ensure the accuracy of the printing pattern and reduce the occurrence of moiré and overprint characters on the pattern while avoiding the production of static electricity, the tension of the disc is as high as 26N/cm, and the mesh distance is as small as 1.0mm. If the screen is printed under the above conditions, static electricity may still appear. At this time, adjustment of the squeegee speed may be avoided.
Screen printing environment conditions matching, screen printing better printing environment temperature at 23 °C ± 2 °C relative humidity of 60% -70%, which solvent solvent evaporation speed control, good control of the viscosity of UV light solid ink favorable , Stabilize the viscosity of the ink, you can meet the printability of the ink, ink printability is not good because the ink itself appears to pull the wire phenomenon.
Second, if the above process conditions are in place, then the static control methods are:
1. The workpiece itself is charged. At this point, the static elimination device may be used to destaticize the surface of the device prior to screen printing. The method is very simple; use the static elimination equipment to eliminate static electricity on the surface of the workpiece and print it after processing.
2. Screen printing plastic workpieces with static electricity. Antistatic agents can be added to plastic formulations in advance, which requires the production of plastic raw material suppliers.
3. It is also possible to eliminate the static electricity by adding an anti-static coating on the surface of the electrostatically charged workpiece.
4. Reasonable use of ink solvents. Even if the ink solvent mixing performance is good, and the conductivity of the solvent is good to adjust the ink viscosity.
5. Increase the grounding of the workpiece from the screen printing equipment so that the charge is released and static electricity is eliminated.
6. In the non-control measures wet screen printing workshop. In the low-humidity season, water splashing to the ground is increased, and the humidity of the screen printing environment during the evaporation process of the local surface is adjusted. This method has no humidity control equipment,
The simple production units are used in many ways. Apart from the humidity control, they also have the effect of preventing the dust in the control.
In short, for the generation and elimination of static electricity, specific conditions and conditions should be analyzed and corresponding measures should be taken so that the printing work can be carried out smoothly and smoothly under the guarantee of product quality.